Stretchable Interconnects
Liquid Wire™ interconnects are made for the toughest mechanical environments—where space is tight, movement is complex, and failure is not an option.
Powered by our patented Metal Gel™, they stretch, flex, and twist through millions of cycles while performing reliably.
Use them to replace failure-prone cables or to simplify designs that would otherwise be limited by the constraints of copper and flex circuits.
Versatile Connection Solutions
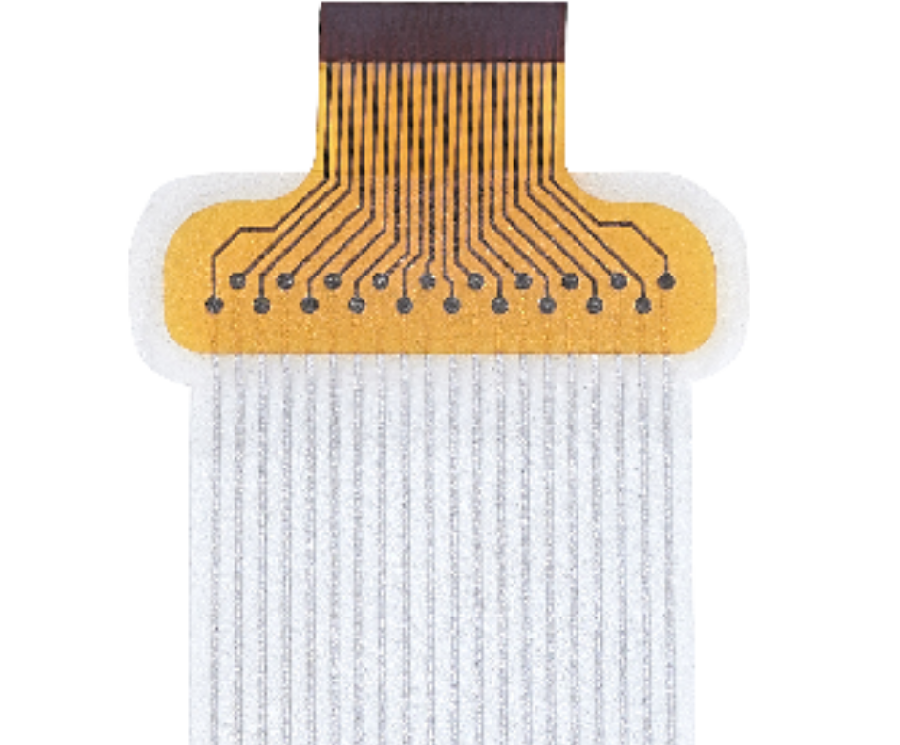
Copper Flex
Flex Polyimide Board with Copper Contact Pads.
For direct soldering.
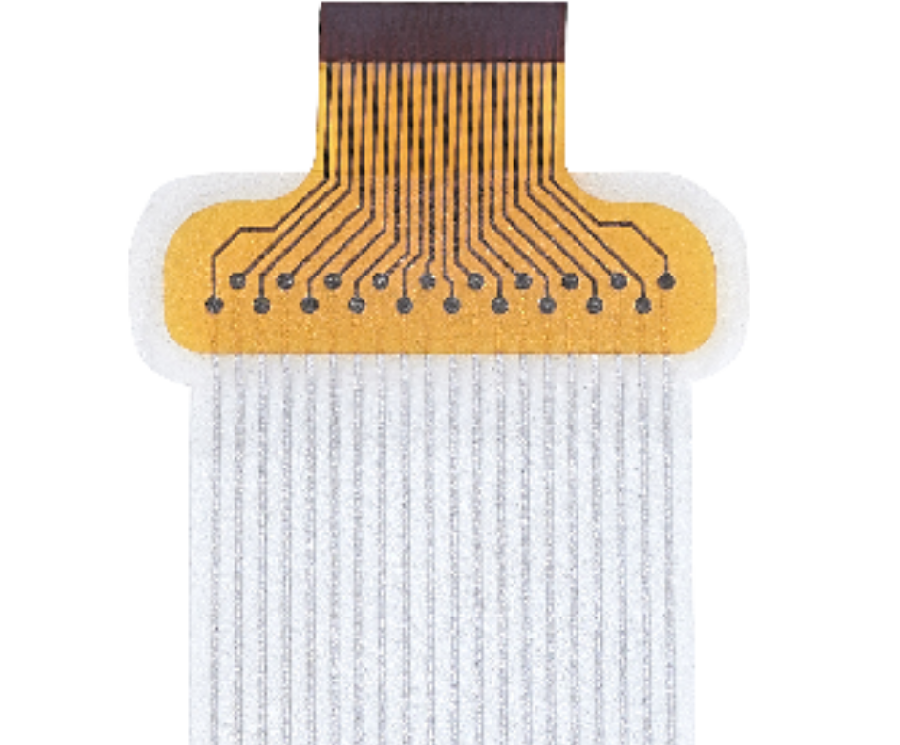
Flex Polyimide Board with Wire Leads
Pre-soldered wire leads for easy connection.
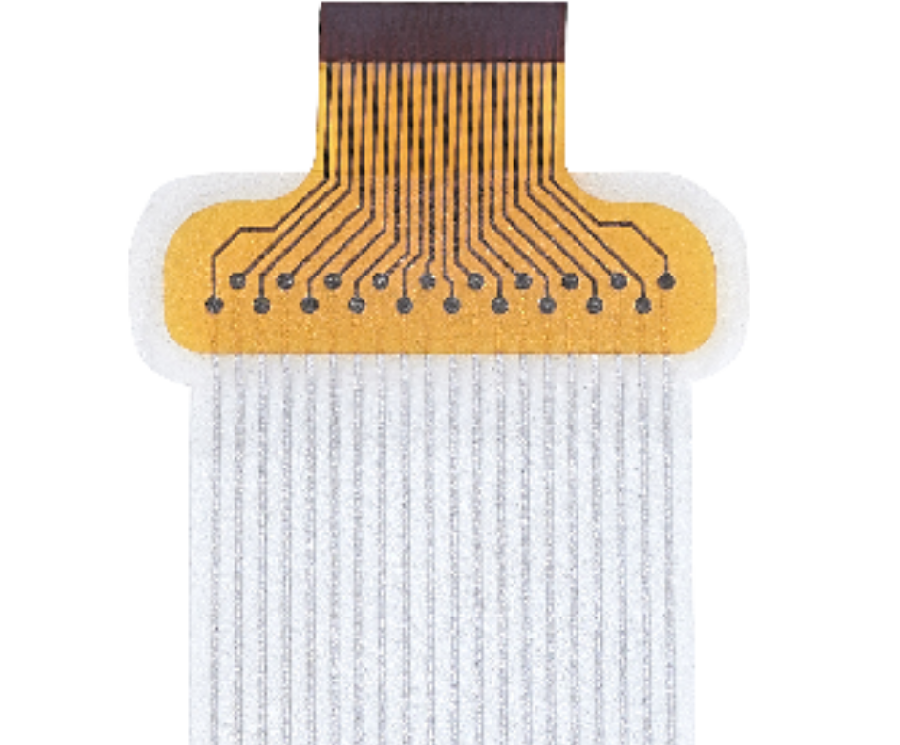
ZIF Connectors
For simple, solder-free connections.
Conductivity Without Compromise.
Liquid Wire™ stretchable interconnects are built for dynamic systems where traditional flex and rigid circuits fail. Powered by our patented Metal Gel™ conductor, they deliver reliable signal and power through millions of movement cycles — enduring stretches, bends, twists, folds, and compression without fatigue or failure.
Key Advantages:
-
Survives Complex Motion: Maintains performance through bends, folds, multi-axis movement, and extreme deformation.
-
.2mm Bend Radius: Routes through tight spaces and moving parts without cracking or delaminating.
-
Ultra Durable: Withstands millions of cycles without loss of conductivity or mechanical failure.
-
Design Freedom: Eliminate the need for bulky strain reliefs or rigid structures.
-
Customizable: Tailored geometries and layouts to match the exact motion profile of your application.
Applications:
-
Humanoid Robotics: Reliable connections through hands, joints, torsos, and spines.
-
Medical Devices: Flexible, body-conforming interconnects for wearables and implants.
-
Industrial Equipment: Survives continuous vibration, flexing, and mechanical stress.
-
Defense and Aerospace: Built for rugged environments — flight, launch, and impact forces.
Liquid Wire interconnects open new possibilities for performance, durability, and freedom of movement — with the ruggedness today’s technologies demand.
Flexibility and Stretchability
One of the most significant advantages of metal gel-based interconnects is their ability to stretch, flex, and conform to dynamic surfaces without compromising their electrical properties.
The gel matrix allows for natural movement, making these interconnects ideal for applications which require dynamic flexure, compression, folding, stretching, thermoforming operations, and extremely tight radii.
The overall mechanical characteristics of Liquid Wire’s interconnect closer matches the characteristics of a polymer substrate rather than a metal or silicon component.
Mechanical Durability:
Liquid Wire’s interconnects can withstand millions of stretch and bend cycles without appreciable loss in performance.
Liquid Wire interconnects are nominally designed for up to 30% strain. Please contact Liquid Wire to inquire about a customized solution if greater elastic strain tolerance is required.
Environmental Resistance
Our current manufacturing process has high survivability and should survive to 65 wash/dry cycles and beyond, dependent on needed electrical performance.
Temperature Stability
Metal Gel Freezes at –20 degrees Celsius and can be brought back to a fluid state at 11 degrees Celsius. The higher end of the thermal range is defined by the characteristics of the substrate. The TPU used for Liquid Wire Interconnects has been tested to 60 degrees Celsius (dynamic) and 100 degrees Celsius (static).
Design Considerations
The performance of a Metal Gel-based interconnect depends not only on its material properties but also on its dimensions and placement within the system.
Choosing the Right Dimensions
The size, shape, and aspect ratio of the interconnect can affect its successful integration within the system.
Length (L):
Structures can be laminated together to create extended-length interconnect structures. However each section must conform to the maximum single-structure dimensions of 350mm x 238mm.
Trace Width (Wt):
The Trace Width is the width of the metal gel inside the structure.
Web Width (Ww):
The web width is defined as the width of polymer that separates the traces of metal gel. Below is an example of a strain sensor with a web width of 4.6mm.
Trace Width (Wt):
Trace Width | Recommendation |
0.3 mm | Minimum |
0.5 mm | Preferred |
2.0 mm | Maximum |
Web Width (Ww)
Trace Width | Recommendation |
1.0 mm | Minimum |
3.0 mm | Preferred |
N/A | Maximum |
Thickness (T):
Liquid Wire’s interconnects use metal gel traces that are nominally 0.1mm thick. Variations on thickness can be achieved with custom layups.
Border Requirements:
There are minimum polymer widths between the edge of the metal trace and the extents of the structure itself. The standard border is 3mm.
Optimizing Interconnects
Since the nominal conductivity of the metal gel is just over 3% that of copper, depending on the application multiple traces or increased trace size can be used to reduce the overall resistance of the conductor.
Hardware Interface
Standard Liquid Wire interconnects have these primary options for termination:
- Molex 5035520622 Plug / Molex 5035480622 Receptacle
- Molex Pico EZmate (2,4,6 pin)
- ZIF (Hirose FH34SRJ-16S-0.5SH(50) 16 pin / TF31-6S-1SH(800) 6 pin
- Solder Pads
- Mezzanine
- FR4 Direct Attach
Inquire with Liquid Wire about your preferred termination that is not listed.
Interconnect Performance
When the structure is deformed (stretched, flexed, folded, etc.) in application, a very small change in resistance occurs. This is due to the cross-sectional variation induced by the associated Poisson’s Ratio of the polymer substrate.
The change in resistance during strain for a nominal structure is linear, and can be calculated by multiplying the initial resistance of the structure, the percentage of strain, and 1.15.
Explained by example, for a standard 0.5mm wide trace with 0.1mm thickness one could expect a nominal resistance of 10.51 Ω at 1 meter length. If that single trace were to increase 10%, we would expect a resistance change as follows:
ΔR = 10.51Ω*0.1*1.15 = 1.20865Ω.
Hysteresis
Hysteresis occurs when a structure’s resistance does not follow the same path for increasing and decreasing strain. While Metal Gel itself does not exhibit hysteresis, the constructed sensor assembly is subject to the performance of the polymer with which it is constructed. Note the change in resistance of the interconnect is very small, however it may be a consideration for certain applications.
Below is a chart of a Metal Gel structure’s measured resistance during a 1 million cycle, 30% test:
Note during periods of rest with no force on the conductor there is a slight slope to the resistance where the polymer is recovering.
Modifications to the structure can be made to improve performance depending on application requirements. Contact Liquid Wire for specific options to improve performance.
Thermal Effects on Conductivity / Resistance
Temperature fluctuations can cause material expansion and resistance changes.
The nominal temperature coefficient for metal gel is defined as:
α=3.017×10−3 K−1
Interconnect Resistance
Liquid Wire interconnects typically have a nominal resistance in the single to double-digit ohm range, however the specific design will dictate nominal resistance.
Communication Protocol
The electrical characteristics of each structure are unique based on its geometry; however, the structures are commonly used for inter-IC communication protocols such as SPI and I2C.
Designs requiring Ethernet or similar protocols require more precise impedance control.
Impedance Control
Liquid Wire’s Metal Gel structures have been built for use in RF applications (NFC antennae, etc.) and high speed communication for highly specific applications. -3dB points at 3GHz have been achieved, however these applications typically require an engineering effort outside the scope of this document.
For applications requiring precise control of impedance please reach out to Liquid Wire for more information.
Assembly Considerations
The ZIF connection and solder pad terminations of the structure are not intended to accommodate the forces generated by applying strain to the structure. As a result, application designers should take care to provide strain relief to the connection.
Textile Strain Relief
Due to the unique construction process of the Liquid Wire interconnects, certain textiles can be added into the structure to provide an attachment method. An example of marquisette integration is shown below.
If your application requires the integration of a strain relief textile, please contact Liquid Wire for more details.
Strain Relief
Addition of eyelets or other 2-D features in the polymer can be used to anchor each end of the interconnect.
Stitching
Due to the low durometer and slim design of the interconnect structure, stitching can be used to adhere the sensor to the application.
Lamination
It is possible to laminate Liquid Wire structures to soft goods. The specific procedure is dependent on the application fabric and structure details. Please contact Liquid Wire for more information.
Metal Gel Properties
Summary Table
Property |
Value |
Units |
Resistivity |
4.7 x 10-7 |
Ωm |
Operating Temperature (Dynamic structure) |
-20 to 60 |
oC |
Operating Temperature (Static structure) |
-60 to135 |
oC |
Strain limit with TPU |
30 |
% |
Hysteresis |
|
Minimal |
Minimum Bend Radius |
<1 |
mm |
Wash/Dry Durability |
65+ |
cycles |
Reliability |
>1,000,000 |
Cycles |
Maximum Operating Current* |
800 |
mA |
Maximum Frequency** |
3 |
GHz |
Figure 1. Table
* For a standard trace 0.6mm wide by 0.1mm deep – for higher current applications contact Liquid Wire for assistance
** 3GHz 3dB point was achieved using a multi-layer structure. For specific application information and requirements contact Liquid Wire for assistance.
Hands-On Access to Deformable Circuits with Evaluation Kits
Domestic & International Shipping Available
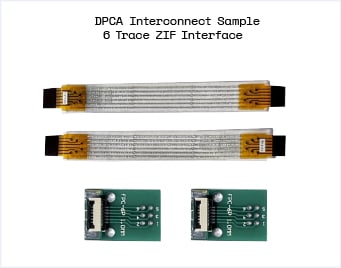
Stretchable Interconnect, ZIF Termination with Breakout Boards
Evaluation Kit
$199/ additional samples available
Built to assess behavior under stress and real-world performance.
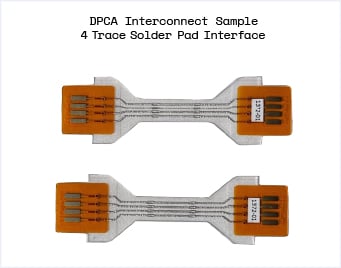
Stretchable Interconnect, Solder Pad Termination
Evaluation Kit
$199/ additional samples available
Built to assess behavior under stress and real-world performance.
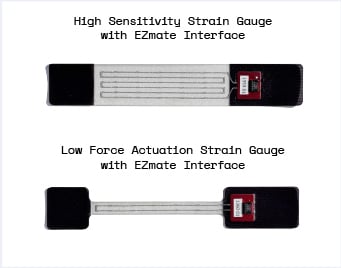
Stretchable Strain Sensor, High Sensitivity & Low Force
Evaluation Kit
$499/ additional samples available
Built to assess behavior under stress and real-world performance.