Stretchable Strain Sensors
Made for the toughest mechanical environments—where space is tight, movement is complex, and failure is not an option.
Liquid Wire™ strain sensors built with Metal Gel™ provide reliable, high-resolution measurements of mechanical deformation even when stretching, flexing, or twisting; they conform to dynamic systems and survive millions of cycles, enabling precise, durable sensing in robotics, medical devices, wearables, and industrial equipment.
Versatile Connection Solutions
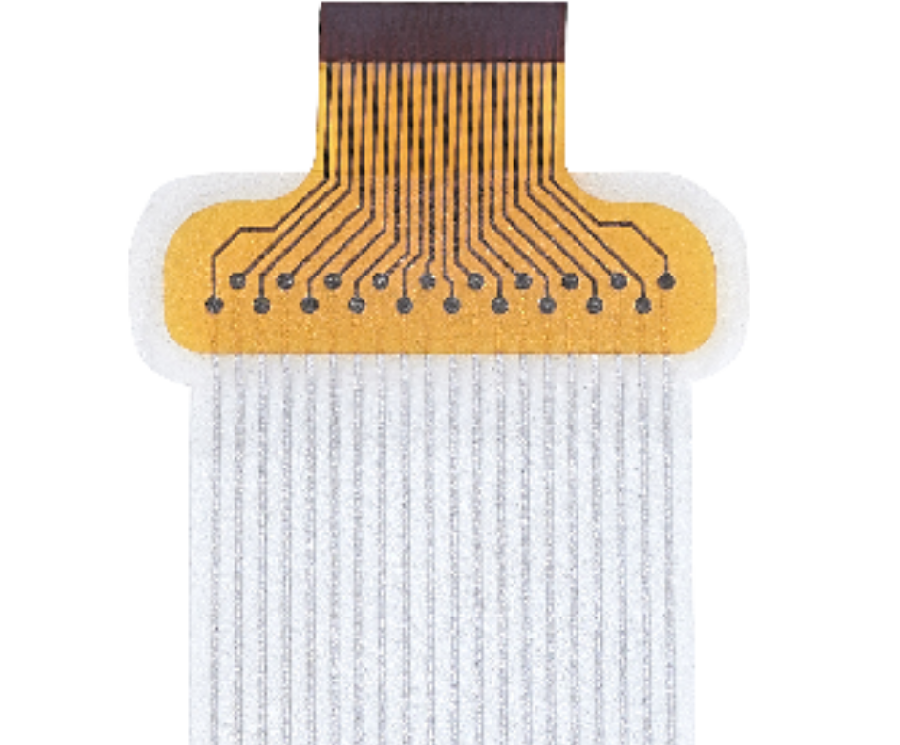
Copper Flex
Flex Polyimide Board with Copper Contact Pads.
For direct soldering.
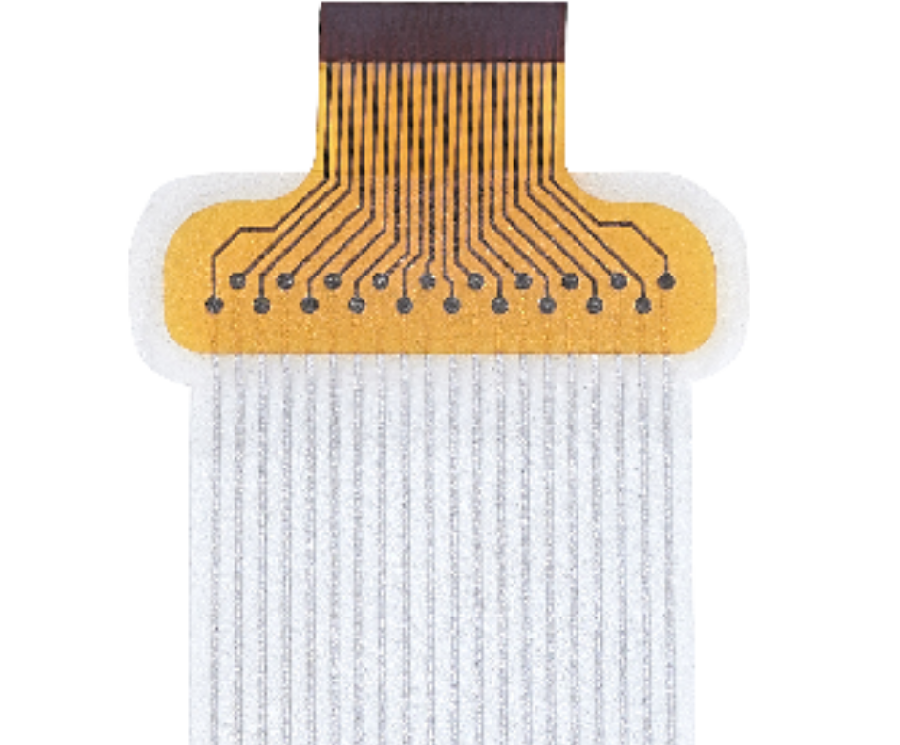
Flex Polyimide Board with Wire Leads
Pre-soldered wire leads for easy connection.
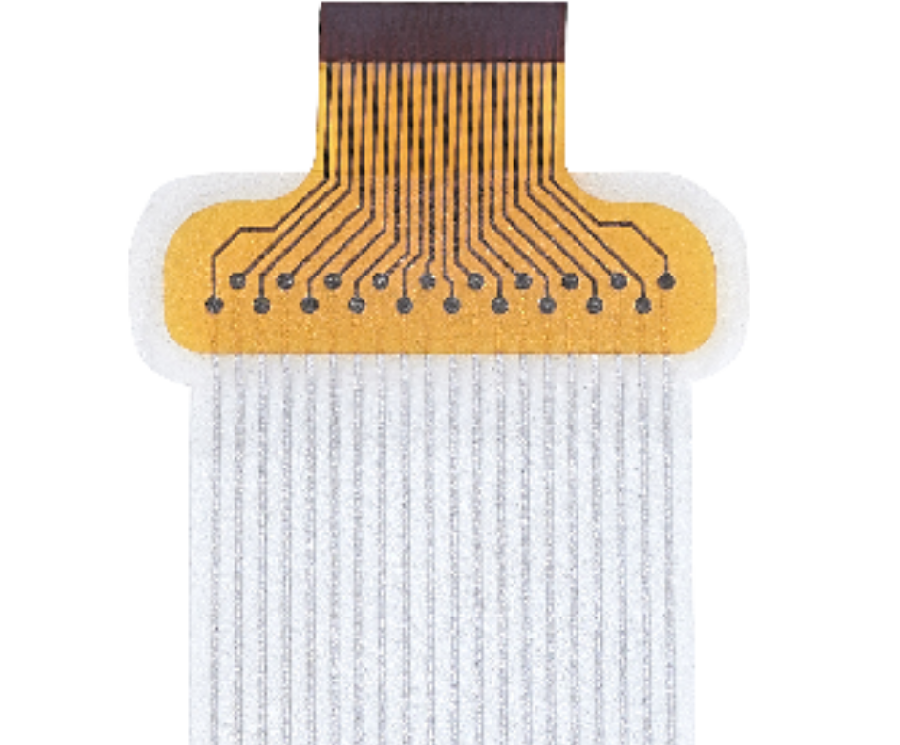
ZIF Connectors
For simple, solder-free connections.
Measure What You Couldn't Before
With highly flexible and stretchable Metal Gel™ circuitry, Liquid Wire™ Stretchable Strain Sensors exhibit a change in resistance under strain, enabling them to detect tensile or compressive sub-millimeter movement—typically outside the realm of what is measurable with conventional sensors.
Millions of Cycles at 30% Elongation Without Performance Degradation
While many strain sensors fail past 5 or 10% strain, Liquid Wire™ sensors can be cycled repeatedly to 30+%. Coupled with a low-cost precision current source, this sensor can detect sub-millimeter changes in length with near-zero hysteresis.
Truly Deformable
Crafted from Metal Gel™, a proprietary liquid metal alloy, and embedded in a robust thermoplastic laminate structure, our strain sensors can stretch and flex without compromising their integrity.
Stretch
Deform
Bend
Compress
Low Hysteresis
Reliable Connectivity
Moreover, the same Metal Gel™ conductor that measures strain can simultaneously transmit digital data on established protocols like I2C, USB, and SPI. The resistance and impedance changes are easily detectable but have negligible effects on digital signal transmission, ensuring no disruption to the electrical system's function.
RoHS Compliant
Strain Sensor Applications
Liquid Wire™ Stretchable Strain Sensors are engineered for high-performance motion and deformation tracking across dynamic environments. Their flexible, durable construction makes them ideal for:
Robotics
Joint monitoring, flexible joints.
Wearables
Monitor body movements including breathing, track fitness activities, and provide valuable health insights with smart garments.
Medical
Rehabilitation, movement analysis, & prosthetics.
Industrial
Monitor strain and position in machinery and equipment, ensuring optimal performance and safety.
Defense
Body-worn electronics, motion analysis under load.
Research
Researchers can leverage our sensors in various experimental setups to gather accurate strain data, driving innovation in multiple fields.
Understanding Strain Gauge Basics
Strain is a measure of deformation in a material when subjected to an external force. It is defined as the ratio of the change in length, to the original length of a material, and is expressed as a dimensionless unit.
where:
ε = strain
ΔL = change in length due to applied force (m) L₀ = original length of the material (m)
Fundamental Principles of
Strain Gauge Operation
A strain gauge operates on the principle that a material’s electrical resistance changes when it undergoes mechanical deformation:
where:
R = electrical resistance (Ω)
ρ = resistivity of the material (Ω·m)
Note: The resistivity of Liquid Wire’s Metal Gel is approximately 4.75x10–⁷
L = length of the conductor (m)
A = cross-sectional area (m²)
• Nominal depth of traces in a Metal Gel structure is 0.1 mm
• Nominal width of traces in a Metal Gel structure is 0.5 mm
When a strain gauge is stretched L increases, A decreases, causing R to increase. The sensitivity of a strain gauge is defined by:
where:
GF = gauge factor (unitless)
ΔR = change in resistance due to strain (Ω) R₀ = original resistance of the strain gauge (Ω) ε = applied strain (unitless) A higher gauge factor means greater sensitivity to strain.
Flexibility and Stretchability
One of the most significant advantages of Metal Gel-based strain gauges is their ability to stretch, flex, and conform to dynamic surfaces without compromising their electrical properties. They can endure strain exceeding 30% or more. The polymer matrix allows for natural movement, making these sensors ideal for applications requiring dynamic flexure, compression, folding, stretching, thermoforming operations, and extremely tight radii. Under repeated bending, stretching, and twisting, Metal Gel maintains its conductivity and sensitivity. The overall mechanical charac-teristics of Liquid Wire’s strain sensors more closely match the characteristics of the polymer substrate, rather than a metal or silicon component.
Sensitivity
The Metal Gel’s composition can be engineered to optimize sensitivity for specific applications. Multiple factors including
the number of traces crossing the strain area, trace dimensions, and overall sensor geometry. This offers flexibility in determining the sensor’s sensitivity level.
Tunable Sensitive Regions
Liquid Wire’s structures can be created in a manner that allows for a specific section of the structure to be sensitive to strain, while other locations are not. This is accomplished using Kelvin Sensing.
Mechanical Durability
Liquid Wire’s strain sensors can withstand millions of strain cycles, depending on application, without significant loss in performance. They are nominally designed for repeated strain up to 30% with no plastic deformation. Applications that require much higher amounts strain are possible but may plastically deform the structure.
Washability
Our current structures have high survivability and will survive over 65 wash/dry cycles.
Low Temperature Stability
Metal Gel freezes at –20 °C and can be brought back to a fluid state at 11 °C.
Note: the Metal Gel will still conduct while in its frozen state. If it is stretched or deformed while frozen, cracks may be induced and cause open circuits. In some applications these cracks recover—contact Liquid Wire for application assistance while using Metal Gel below –20 °C.
Placement
Proper sensor dimensioning and placement ensure accurate strain measurements, while effective electrical interfacing and signal conditioning enhance the quality of the data. The performance of a Metal Gel-based strain sensor depends not only on its properties
but also on its placement within the system. Proper sensor design ensures accurate, reliable strain measurements while minimizing errors due to external influences.
Choosing the Right Sensor Dimensions
The size, shape, and aspect ratio of the strain gauge affects its sensitivity, resolution, and integration within the system.
Structure Length (L)
Structures can be laminated together to create extended length, however each section of the structure must conform to the maximum single-structure dimensions
of 350 mm x 238 mm.
Trace Width (Wt)
The trace width is the width of the Metal Gel inside the structure.
Trace Width (Wt)
The trace width is the width of the Metal Gel inside the structure.
Thickness (T)
Liquid Wire’s strain gauges use Metal Gel traces that are nominally 0.1 mm thick. Variations on thickness can be achieved with custom layups.
Border Requirements
There are minimum polymer widths between the edge of the Metal Gel trace and the extents of the structure itself.
Optimizing Sensor Response
The average gauge factor for a Metal Gel strain gauge, calculated by averaging all measured values, is 1.15 ± 0.07.
The change in resistance can therefore be calculated using the following formula:
ΔR = (1+ %change/100 ) x GF
Explained by example, for a standard 0.5 mm wide trace with 0.1 mm thickness one could expect a nominal resistance of 10.51 Ω/m. If that single trace were to increase 10%, we would expect a gain as follows:
ΔR = (1+0.1)*1.15 = 1.265Ω.
In cases where increased sensitivity is required, multiple passes of the metal gel trace through the strain region can be used:
A 2-pass Strain Sensor
In the case of the above sensor, there are two passes of the Metal Gel through the active region. The same calculation for change in resistance can be performed, however due to multiple passes through the same strain region the change in resistance is multiplied by the number of traces:
Explained by a different example, for a standard 0.5 mm wide trace with 0.1 mm thickness one could expect a nominal resistance of 10.51 Ω/m. Assume an active region length of 100 mm. This would result in a nominal resistance of 1.51 Ω/100 mm. Since we have multiple passes of 100 mm in Figure 2 above, our total trace length is ~200 mm (not accounting for the short vertical portion). If that single trace were to increase 10%, we would expect a 20% gain in the total trace length – resulting in the following:
ΔR = (1+2*0.1)*1.15 = 1.265Ω.
ΔR = (1+ %change/100 ) x GF
An 8-pass Strain Sensor
Strain and resistance performance for this 8-trace structure are shown below.
Hysteresis
Hysteresis occurs when a sensor’s output does not follow the same path for increasing and decreasing strain, leading to errors in measurement. The constructed sensor assembly is subject to the performance of the polymer with which it is constructed.
Below is a chart of a Metal Gel structure’s measured resistance during a 1 million cycle, 30% test:
Time vs. Resistance plot of 1,000,000 cycle test
Recovery from Strain
Recovery is the ability of a sensor to return to the same geometry under identical strain conditions at a specific rate.
Liquid Wire Metal Gel sensors use a polymer substrate that has certain characteristics that affect the recovery of the sensor.
Specific strain recovery performance is application dependent. Example data is shown below.
Time vs. Resistance, Displacement, and Force
Note that during periods of rest with no force on the sensor there is a slight slope to the resistance where the polymer is recovering. This recovery property of the polymer should be taken into consideration for applications requiring high frequency strain application.
Modifications to the sensor structure can be done to improve performance depending on application requirements. Contact Liquid Wire for specific options to improve performance.
Thermal Effects on Strain Measurements
Temperature fluctuations can cause material expansion and resistance changes.
The nominal temperature coefficient for Metal Gel is defined as:
α=3.017×10−3 K−1
Using a Kelvin Sensing configuration, Liquid Wire strain sensors can be created that exhibit sensitivity in specific regions, and do not respond to strain in others.
A strain sensor with active and inactive regions.
Liquid Wire strain gauges typically have a nominal resistance in the single to double-digit ohm range, however the specific design will dictate nominal resistance. Strain gauges offered by other manufacturers generally operate in the 100 to 3k ohm resistance range. This large difference in resistance ranges necessitates a different hardware topology to measure the incremental changes in resistance as the material experiences strain.
Reference Circuit:
Due to the low resistance change and relatively high conductivity of the Liqud Wire strain sensors, a Resistance Temperature Detection (RTD) sensing methodology is recommended. This configuration allows for precise sensing of the change in resistance while creating some immunity to noise and minimizing power consumption.
An example circuit is below:
Transfer Function
In the above circuit, the ADC will provide a count value instead of a resistance value, the below equation will provide a resistance value once converted:
Where:
RREF=1k Ohm
Gain = 16 (Firmware dependent)
n (resolution of ADC) = 24 (Hardware dependent)
The ZIF connection and solder pad terminations of the structure are not intended to accommodate the forces generated by applying strain to the structure. As a result application designers should take care to provide strain relief to the connection.
Textile Strain Relief
Due to the unique construction process of the Liquid Wire strain sensors, certain textiles can be added into the structure to provide an attachment method. An example of marquisette integration is shown below.
If your application requires the integration of a strain relief textile please contact Liquid Wire for more details.
Polymer Structure Geometry Strain Relief
Addition of eyelets or other 2-D features in the polymer can be used to anchor each end of the interconnect.
Stitching
Due to the low durometer and slim design of the interconnect structure, stitching can be used to adhere the sensor to the application.
Lamination
It is possible to laminate Liquid Wire structures to soft goods. The specific procedure is dependent on the application fabric and structure details. Please contact Liquid Wire for more information.
Gauge factor | 1.1 – 1.45 |
Sensitivity | Customizable - see app notes |
Operating temp - dynamic structure | -20 to 60 °C |
Operating temp - static structure | -60 - 135 °C |
Nominal strain limit | 30% |
Minimum bend radius | 1 mm |
Wash/dry durability | 65+ cycles |
Life cycle | >1M cycles |
Hands-On Access to Deformable Circuits with Evaluation Kits
Domestic & International Shipping Available
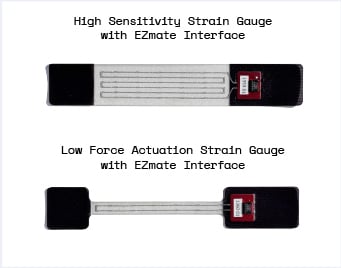
Stretchable Strain Sensor, High Sensitivity & Low Force
Evaluation Kit
$499/ additional samples available
Built to assess behavior under stress and real-world performance.
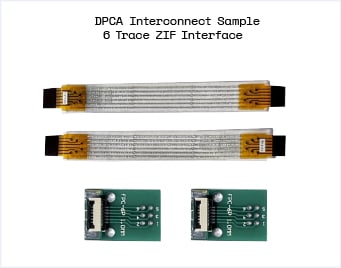
Stretchable Interconnect, ZIF Termination with Breakout Boards
Evaluation Kit
$199/ additional samples available
Built to assess behavior under stress and real-world performance.
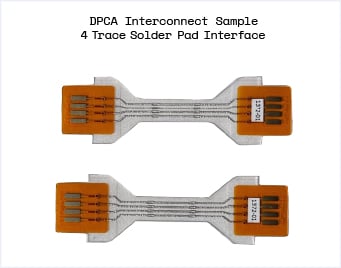
Stretchable Interconnect, Solder Pad Termination
Evaluation Kit
$199/ additional samples available
Built to assess behavior under stress and real-world performance.